Vacuum Casting
Vacuum Casting is a very superior rapid prototyping type for 5-100 unit plastic parts. It usually uses a 3D printing or machined prototype then copy the silicone molds, then pour PU light-sensitive material into the silicone mold to casting the parts. This whole processes happens in a day or even several hours. Usually, for tens of parts, vacuum casting is mach cheaper than CNC machining or 3D printing. WeLink Vacuum Casting can make big parts above 2,000 mm.
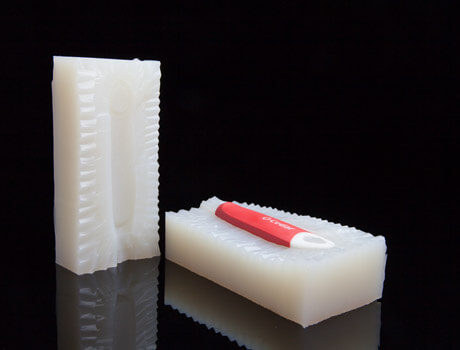
WeLink Vacuum Casting Solutions
Part Size: 10 ~ 3,000 mm
PU material: ABS like, PA like, PP like, PC like, PMMA like, POM like, ABS UL-94 V.., Glass Fiber, etc.
Material Vendor: AXSON, Hei-Cast, etc.
Mold Life: 30-50 shoots for simple and small parts; 20-30 shoots for general parts; 5-10 shoots for complex or big parts
Pricing: WeLink is cost-effective
Lead Time: 2-3 days
What is Vacuum Casting Process?
Vacuum casting (also called resin casting) is a molding method for duplicating plastic products by pouring plastic into a mold contained within a near vacuum tank. This method’s greatest feature is its ability to create highly precise plastic products while reducing cost and drastically minimizing turnaround. Epoxy and urethane plastics are typically used for the mold, and the master mold typically uses silicon or plastic. The plastics used for casting are highly viscous, though many have low liquidity. After the air in the tank is extracted with a pump, creating a vacuum state, the plastic is poured in. The pressure difference is used to spread the plastic to every corner of the master mold as the pressure is gradually returned to normal. WeLink uses a silicon variety for the master mold, processing mainly urethane plastics.
Advantages Of Vacuum Casting
- Low cost for molds
- Molds can be made in a few days
- Many types of polyurethane resins are available for casting, including overmolding
- Cast copies are highly accurate with excellent surface texture
- Molds are durable for 20 or more copies
- Perfect for engineering models, samples, rapid prototypes, bridge to production
Vacuum Casting Tolerances
The finished dimensions of vacuum cast parts are dependent on the accuracy of the master pattern, the part’s geometry and the type of casting material used. Generally a shrinkage rate of 0.15% is to be expected.
Vacuum Casting Materials
Hundreds of casting polymers are commercially available to reproduce any conceivable hardness and surface texture. It is also possible to make parts that are fully opaque, translucent or completely transparent depending on your application.